Navigating The Carbon Exchange Landscape (wateronline.com)
Granular activated carbon (GAC) filters are an increasingly popular technology for removing contaminants from liquid or vapor-state water. To remain effective, carbon media must be replaced periodically. The best way to handle spent carbon depends on a variety of factors, including the application, contaminants adsorbed, local regulations, staff expertise, and more.
This article is designed to help engineers and plant managers determine how best to manage the carbon exchange process, including whether to use virgin or reactivated carbon, when to exchange carbon, and whether the exchange process should be handled in-house or with a third-party vendor.
Understanding Virgin And Reactivated GAC
Virgin carbon comes directly from the manufacturer and has not been exposed to contaminants. Reactivated carbon has been exposed to fluids or vapor and processed through a reactivation kiln to desorb the contaminants. While more cost-effective, reactivated carbon has approximately 10% to 15% less adsorption capacity than an equivalent mass of virgin carbon, due to structural degradation of the carbon and some contaminants failing to desorb in the kiln. As such, some applications that require high-purity effluent, such as municipal drinking water, require virgin carbon.
When To Exchange Carbon
Most liquid-phase applications have a lead-lag vessel configuration (Figure 1). The leading edge of the mass transfer zone (MTZ) is where adsorption capacity is full and contaminant breakthrough occurs. Operators should take samples to track where the leading and lagging edges are advancing within the media bed. Ideally, a changeout should be scheduled when the leading edge is well through the lag vessel but not eclipsing it. Of course, applications with more stringent water quality requirements may schedule their exchange sooner.

Figure 1. An example of a lead-lag vessel configuration. To get the most out of the carbon, an operator should take samples to track where contaminant breakthrough occurs (leading edge), as well as where the lagging edge is (where adsorption is just beginning) and how much of the carbon is saturated in the lead vessel. The goal is to time the exchange when the leading edge of the breakthrough is well through the lag vessel but not eclipsing it. If water quality requirements are more stringent, operators may want to schedule an exchange when the lead vessel has reached a predetermined percentage of saturation, or at the first sign of a breakthrough in the lag vessel.
Vapor-phase applications have a much smaller MTZ than liquid-phase applications. Operators can use a breakthrough indicator, which will detect contaminant breakthroughs at 75% to 90% bed depth. Again, based on purity requirements, operators can schedule a carbon exchange at various points, such as when the indicator is positive or when a breakthrough is first detectable and measurable.
Who Will Perform The Exchange?
When adopting a GAC system, plant managers must decide if carbon exchanges will be performed by in-house personnel or a vendor. Carbon exchanges are often done in-house for the convenience of scheduling as needed and/or to combine with routine maintenance.
However, there are several critical downsides to performing an in-house carbon exchange, such as:
- Carbon supply. Operators have to purchase or maintain inventory of sufficient quantities of carbon. If kept in inventory, space must be allocated for storage. Alternatively, if carbon is ordered on demand, operations could suffer from potential supply problems or delays in shipping.
- Equipment requirements. Whether performing a slurry exchange or vacuuming the vessels, the proper equipment — including personal protective equipment (PPE) — must be used. This can be costly, as it requires an initial capital investment in the equipment itself, as well as the cost of training operators in their use and maintenance.
- Removal expertise. In addition to knowing how to use the equipment, operators need to understand how to remove and replace carbon without damaging the vessels. As mentioned above, carbon can be removed using a slurry method, in which the carbon is kept wet and then pressurized to move it through a valve and into a tanker. The vacuum method (Figure 2) works for smaller amounts (less than 10,000 lbs.) and requires draining all water from the carbon and sucking the dry media out of the vessel and blowing it into a supersack.
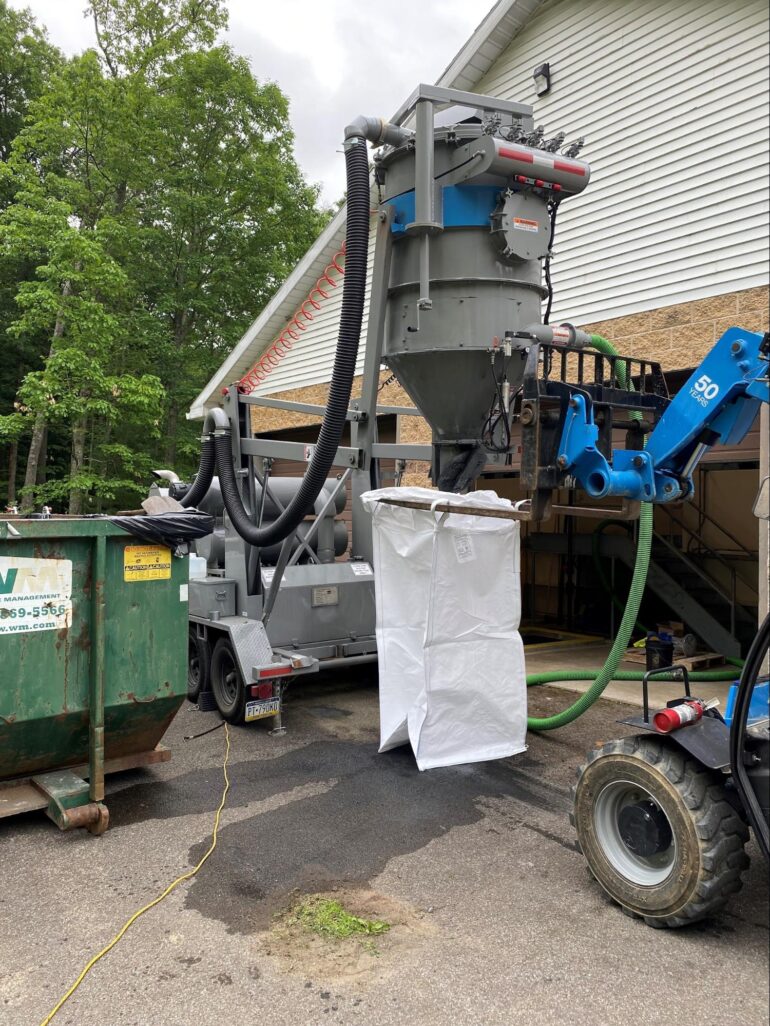
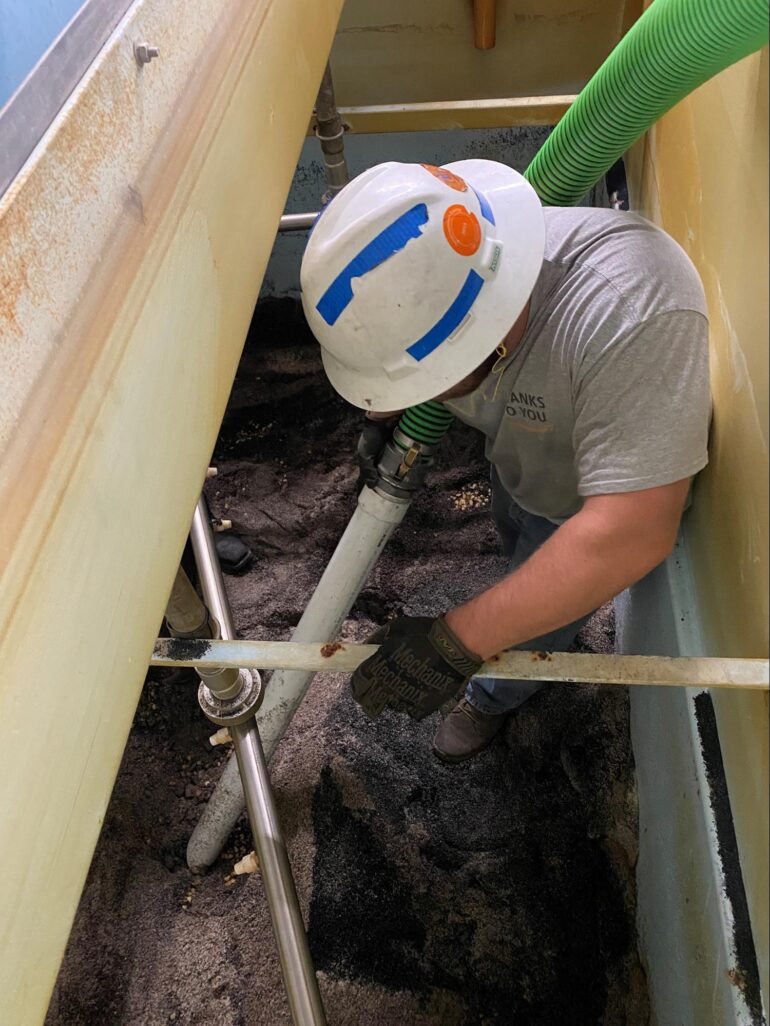
Figure 2. On the left, a trained carbon exchange expert vacuums up spent carbon from the vessel, where it is then ejected into a supersack (right) for transporting and disposal.
Using a carbon exchange service avoids many of these challenges. Service providers have highly trained teams with the proper PPE and equipment for the site and application. In addition to removing the carbon, vendors can also provide multi-point inspections of the vessel to ensure its integrity before adding new media.
Carbon exchange service providers eliminate the need to store carbon onsite and prep the spent carbon for disposal. In addition, service providers can complete disposal certification as required by regulations.
Choosing A Disposal Method
There are three ways to dispose of spent carbon media. The process used will depend on the contaminants adsorbed and their concentration. A Toxicity Characteristics Leaching Procedure (TCLP) analysis can determine if the spent carbon is classified as hazardous or non-hazardous waste.
- Reactivation. As mentioned above, this process involves exposing the carbon to heat in a kiln to desorb the contaminants. Regulations may prohibit the reactivation of carbon containing hazardous contaminants or concentrations of compounds such as polychlorinated biphenyls (PCBs).
- Landfill. The seemingly simplest disposal method, landfilling carbon is an option provided the media is classified as non-hazardous and does not contain high concentrations of regulated contaminants that can leach into the soil, such as arsenic, antimony, or other Resource Recovery and Conservation Act (RCRA) metals.
- Incineration. If necessary, GAC can be destroyed by incineration. This is often necessary for contaminants such as PCBs and pesticides. However, this process produces a large amount of greenhouse gases and can work against the plant’s sustainability goals.
The most challenging part of the carbon exchange process can often be figuring out which disposal method is the most affordable, practical, and compliant with relevant (and ever-changing) regulations. A carbon exchange service can eliminate this burden by determining the most feasible and legal option and executing it. By trusting a carbon exchange service provider, water treatment professionals can save time and money, leaving personnel free to perform operation-critical tasks.
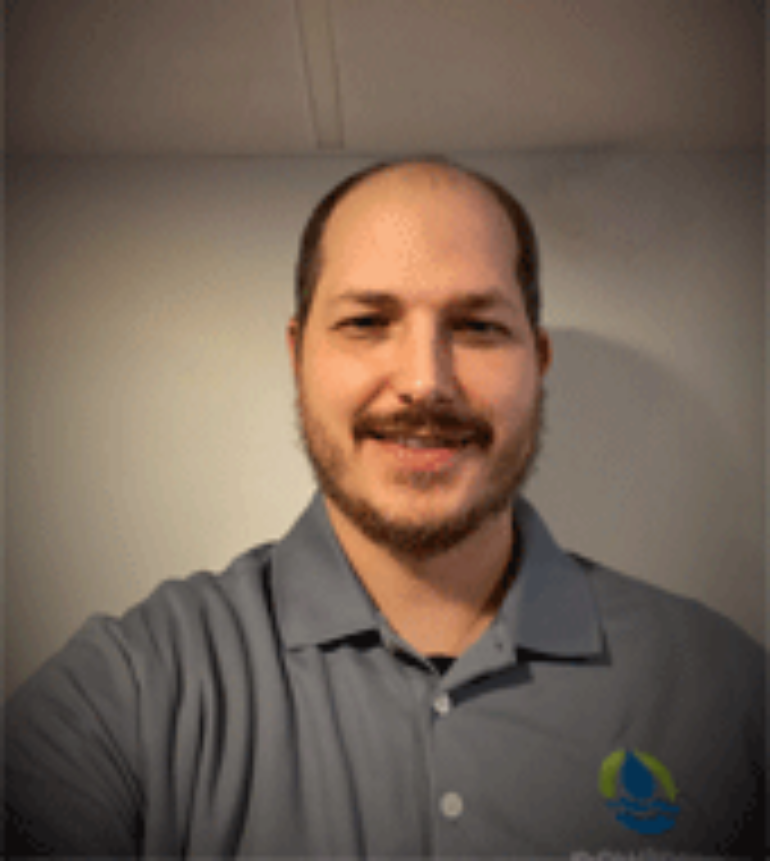
Adam Sattler is the media service product manager at Newterra, an environmental, water and wastewater treatment company. Adam has ten years of experience specializing in media exchanges and servicing industries and municipalities with proper carbon media utilization. In his previous role with Newterra, he served as a Field Service Technician and LifeCycle Account Manager for the Newterra TIGG brand family. Before joining Newterra in 2017, Adam spent five years with Encotech. Mr. Sattler holds a Bachelor’s Degree in Finance from Waynesburg University.
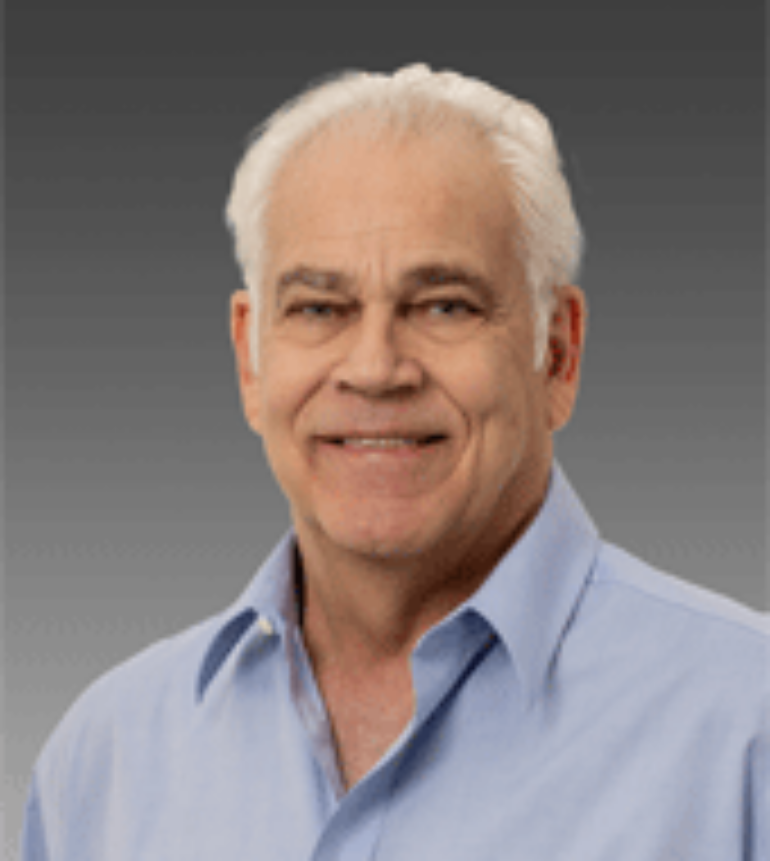
David Woods is a Lifecycle Sales Engineer at Newterra, an environmental, water and wastewater treatment company. With over 20 years in water treatment, his water and carbon technology expertise allows him to provide the best adsorption media and process solutions. David holds a Chemical Engineering degree from Arizona State and started his career at US Steel. He also managed a regional industrial water treatment and process chemical company. With Newterra, David collaborates with remediation customers to solve removing required organic and inorganic contaminants from liquid and vapor streams.