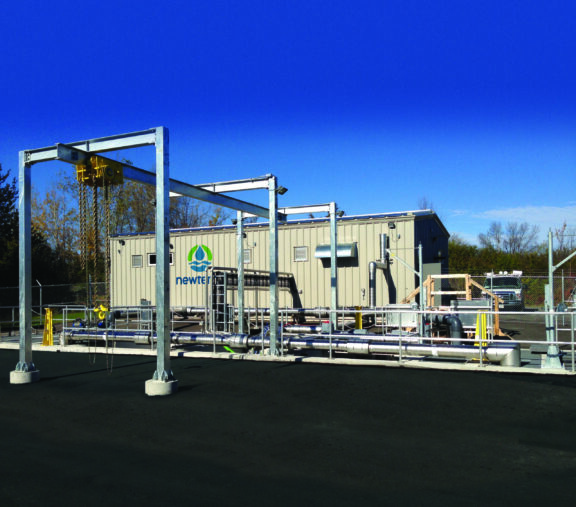
Clear³ MBR.MF Custom Modular Membrane Bioreactor Facilities
Custom, Scalable, and Prefabricated, Newterra Clear3 MBR.MF Custom Modular Membrane Bioreactor Facilities
Read More about Clear³ MBR.MF Custom Modular Membrane Bioreactor FacilitiesThe Argos Sequencing Batch Reactor (SBR) is a True Batch SBR system that combines capabilities of anaerobic, anoxic, aerobic, and secondary clarification into one basin. Powered by the ever-reliable Triton 2.0 Aerator, the Argos combines the safety, convenience, and cost savings of surface-accessible aeration and mixing with the long-time expectation of fine-bubble subsurface aeration associated with traditional methods.
The Argos SBR is an ideal system for municipal and industrial wastewater treatment facilities looking for a user-friendly, energy efficient solution. The Newterra process engineering team provides custom SBR designs specific to the loading information, effluent requirements, and site conditions for any particular site.
The Argos Sequencing Batch Reactor (SBR) is a True Batch SBR system that combines capabilities of anaerobic, anoxic, aerobic, and secondary clarification into one basin. A True Batch SBR, unlike a Continuous Flow SBR, provides a consistent cycle structure within a circular, rectangular, or square basin. A Continuous Flow SBR requires a long rectangular basin to avoid pollutant “short circuiting” and has unpredictable cycle times since it is dependent on the flow.
All components provided with the Argos® SBR are accessible from the surface, which include:
Equalization Basins and aerobic sludge digesters can be packaged with the Argos Sequencing Batch Reactor (SBR) as well.
Argos SBR is an ideal system for municipal and industrial wastewater treatment facilities looking for a user-friendly, energy efficient solution. Aeration Industries process engineering team provides custom SBR designs specific to the loading information, effluent requirements, and site conditions for any particular site.
We understand your unique challenges. Beyond a technology solution, Newterra is dedicated to the entire lifecycle of your needs. Whatever support you need, Newterra probably has a solution to solve it..
Whether your needs are short-term bridge, emergency or supplemental or long-term system deployment, Newterra has flexible solutions that alleviate the need for major capital expenditure.
From operations consultation and long-term service contracts embowered by our Internet of Things (IoT) platform to commissioning expertise and emergency ad-hoc needs almost anywhere in the world, our technical experts are available to serve you. Let Newterra keep your systems optimized.
From licensed and certified removal, to exchange, to supply, Newterra provides the gamut of services to keep your media and membrane solutions at peak performance. Let the same experts who build your systems help you keep them running.
Rely on Newterra for all your aftermarket needs. Our teams have the background and tools to serve you effectively. Nothing beats original equipment manufacturer (OEM) service. Anything you need, we’re here for you.
Custom, Scalable, and Prefabricated, Newterra Clear3 MBR.MF Custom Modular Membrane Bioreactor Facilities
Read More about Clear³ MBR.MF Custom Modular Membrane Bioreactor FacilitiesNewterra Clear³ MBR.ST Configurable Membrane Bioreactor Decentralized Systems are custom configured for your site with the Clear³ standard treatment modules and either in-ground or above-ground tankage.
Read More about Clear³ MBR.ST Configurable Membrane Bioreactor Decentralized SystemsNewterra Clear³ MBR.WWT Modular Membrane Bioreactor Wastewater and Potable Remote Systems are for remote camps and facilities housing from 30 to 8,000 people.
Read More about Clear³ MBR.WWT Modular Membrane Bioreactor Remote SystemsThe Newterra Tri-Oval Oxidation Ditch System is a subsurface complete mix, looped reactor system that is ideal for municipal and industrial wastewater treatment facilities.
Read More about Tri-Oval Oxidation Ditch SystemNewterra UniSystem Package Wastewater Treatment Plant With installations around the world, Newterra’s High-Rate Activated Sludge (HRAS) and Extended Aeration packaged plant is a gold standard for reliability.
Read More about UniSystem Package Wastewater Treatment Plant