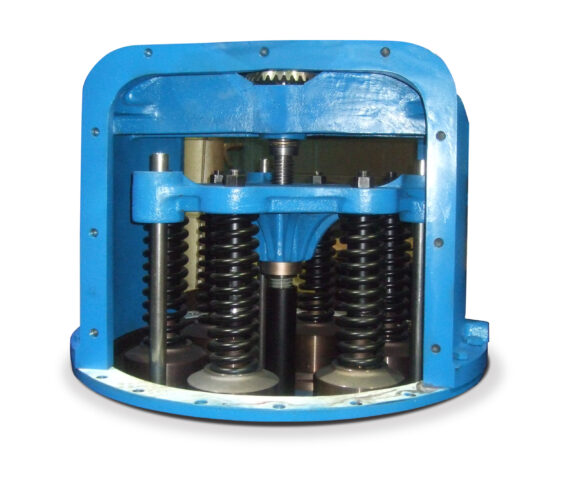
Multiport Relief Valves
Newterra Multiport Relief Valves are designed for safety and to dampen the pressure swings within deaerators, steam lines and associated components.
Read More about Multiport Relief ValvesCounterflow Deaerators are built for reliability in large-capacity industrial applications. Simplicity and a rugged design offer cost savings over a varying load range, especially where a high percentage of condensate returns are introduced. They are American Society of Mechanical Engineers (ASME) stamped and meet Heat Exchange Institute (HEI) requirements.
Newterra’s Counterflow Deaerators epitomize cutting-edge technology in the removal of dissolved gases, primarily oxygen and carbon dioxide, from boiler feedwater to prevent corrosion and enhance the efficiency of steam-generating systems. Featuring a counterflow design, these deaerators maximize contact between water and steam, facilitating exceptional gas removal efficiencies. Tailored for demanding industrial applications, they ensure a consistent supply of high-quality, deaerated water, vital for optimizing the performance and longevity of boilers and steam infrastructure. Newterra’s Counterflow Deaerators are recognized for their operational reliability, energy efficiency, and ease of integration into existing systems, making them an essential component in maintaining the health and efficiency of industrial boiler operations.
We understand your unique challenges. Beyond a technology solution, Newterra is dedicated to the entire lifecycle of your needs. Whatever support you need, Newterra probably has a solution to solve it..
Whether your needs are short-term bridge, emergency or supplemental or long-term system deployment, Newterra has flexible solutions that alleviate the need for major capital expenditure.
From operations consultation and long-term service contracts embowered by our Internet of Things (IoT) platform to commissioning expertise and emergency ad-hoc needs almost anywhere in the world, our technical experts are available to serve you. Let Newterra keep your systems optimized.
From licensed and certified removal, to exchange, to supply, Newterra provides the gamut of services to keep your media and membrane solutions at peak performance. Let the same experts who build your systems help you keep them running.
Rely on Newterra for all your aftermarket needs. Our teams have the background and tools to serve you effectively. Nothing beats original equipment manufacturer (OEM) service. Anything you need, we’re here for you.
Incoming water flows through the spray nozzles and enters the vent condensing chamber as a thin-walled, hollow cone spray pattern. Latent heat transfer is instantaneous because of the intimate water-to-steam exposure.
As the water reaches the tray stack, its temperature is within 2° F of the saturated steam temperature, and virtually all dissolved oxygen and free carbon dioxide have been removed. Nearly all of the steam has now condensed, permitting the non-condensible gases to be carried through the vent by the remaining steam, exiting as a plume.
The preheated water is distributed over the trays and flows down over staggered pans in the trays, making its way through pure steam flowing in the opposite direction. The water leaving the bottom layer of the trays is fully deaerated.
Newterra Multiport Relief Valves are designed for safety and to dampen the pressure swings within deaerators, steam lines and associated components.
Read More about Multiport Relief ValvesNewterra Parallel Downflow Deaerators offer high performance between the extremes of 100% make-up water (below 50° F), mostly hot condensate and substantial flashing returns.
Read More about Parallel Downflow DeaeratorsNewterra Spray Atomizing Deaerators are built for industrial applications to supply high-purity water to maximize the efficiency and lifespan of boiler systems.
Read More about Spray Atomizing DeaeratorNewterra UNI-PAC Packaged Deaerators capacity ranges from 10,000 lbs per hour and larger for parallel downflow, counterflow or spray-atomizing to best suit every application.
Read More about UNI-PAC Packaged DeaeratorNewterra Deaerator and Forced Draft Degasifiers remove dissolved oxygen and carbon dioxide without steam feed or a need for raising water temperature.
Read More about Vacuum Deaerator & Forced Draft Degassifiers